Remain Code-Compliant: Expert Pipeline Welding Inspection Tailored to Your Requirements
Remain Code-Compliant: Expert Pipeline Welding Inspection Tailored to Your Requirements
Blog Article
Necessary Pipeline Welding Evaluation Tips for Quality Control
Exactly how can one guarantee the high quality of these welds that link the pipeline areas? By understanding the necessary pipeline welding examination pointers, specialists can avert prospective threats, decrease pricey repairs, and support the reliability of these vital frameworks.

Importance of Welding Evaluation
Welding inspection plays an essential duty in guaranteeing the architectural honesty and safety of pipe systems. By diligently taking a look at welds, examiners can determine any issues or flaws that could compromise the stability of the pipeline. These inspections are vital for protecting against leaks, ruptures, and various other possibly tragic failures that might lead to environmental damage, monetary losses, and also loss of life.
The significance of welding assessment can not be overstated, as the high quality of welds directly affects the general efficiency and long life of the pipeline. With non-destructive screening techniques such as visual assessment, ultrasonic testing, radiography, and magnetic particle testing, examiners can discover problems that might not show up to the naked eye. By determining and dealing with these issues beforehand, welding evaluation aids to ensure that pipelines fulfill market requirements and regulative needs.
Ultimately, welding assessment is a vital facet of quality control in pipe building and construction, repair, and maintenance (Pipeline Welding Inspection). By maintaining extensive examination criteria, market professionals can mitigate dangers and promote the safety and security and dependability of pipe systems
Usual Welding Defects
Among the obstacles faced in pipeline welding, common defects can significantly impact the structural integrity and performance of the bonded joints. Fractures in the weld can propagate over time, compromising the architectural integrity of the pipeline. Detecting and dealing with these typical flaws with detailed examination and quality control procedures are necessary for ensuring the integrity and safety and security of pipe welds.
Assessment Techniques for Pipelines
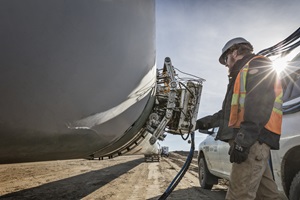

Non-destructive testing (NDT) strategies such as radiographic screening, ultrasonic testing, magnetic particle screening, and liquid penetrant screening are commonly used in pipe welding examination. Aesthetic assessment is also important in pipeline welding to determine any type of noticeable issues or discontinuities. In addition, computerized examination strategies making use of innovative innovations like drones and robotics are progressively being employed to enhance the effectiveness and accuracy of pipeline inspections.
Making Sure High Quality Assurance Criteria
To support stringent top quality guarantee requirements in pipeline building, meticulous adherence to developed sector protocols and guidelines is important. Quality assurance in welding processes requires an extensive approach incorporating numerous stages of pipeline building and construction. Implementing a robust high quality management system that includes normal audits and evaluations can better improve the total high quality assurance standards in pipe welding.
Protecting Against Costly Fixings
Given the vital importance of keeping stringent quality control requirements in pipe construction, a proactive technique to preventing pricey repairs is vital. By implementing complete examination procedures throughout the welding procedure, prospective issues can be determined and corrected beforehand, ultimately saving both money and time. One key facet of protecting against costly repair work is making sure that welders are effectively trained and certified, as this dramatically decreases the possibility of faulty welds that may bring about future failures. Additionally, utilizing advanced inspection methods such as non-destructive screening can assist find any flaws or inconsistencies in the welds before they rise into major troubles. Regular upkeep checks and surveillance of environmental aspects that might impact the stability of the pipe are also crucial in avoiding costly fixings. By buying preventative actions and prioritizing quality control at every stage of the pipeline welding process, business can lessen the danger of expensive repair websites services and ensure the lasting integrity of their framework.
Verdict
In final thought, adherence to appropriate welding examination techniques is vital for ensuring the quality and honesty of pipelines. By identifying usual welding flaws and executing extensive assessment procedures, expensive repair work can be prevented, and quality assurance requirements can be met - Pipeline click resources Welding Inspection. It is crucial for pipe welders to prioritize inspection treatments to maintain the security and dependability of the framework they are working on
The significance of welding examination can not be overstated, as the high quality of welds directly affects the general efficiency and durability of the pipe. Non-destructive testing (NDT) methods such as radiographic testing, ultrasonic screening, magnetic particle testing, and fluid penetrant testing are typically made use of in pipeline welding evaluation. Visual evaluation is additionally important in pipe welding to recognize any type of noticeable issues or gaps. In addition, automatic assessment strategies using innovative modern technologies like drones and robotics are increasingly being employed to enhance the effectiveness and accuracy pop over to these guys of pipe inspections.In conclusion, adherence to appropriate welding examination strategies is crucial for making certain the high quality and integrity of pipes.
Report this page